Our test was somewhat crude, but allowed us to deliver a consistent, repeatable force against an object. We printed identical bars, each with the HackSpace magazine logo on, and each with a hole in each end. We clamped these to a wooden frame so that the bar on the H sat on the surface, then tied a rope onto the hole and applied a force. We gradually increased this force and measured the deflection of the top of the bar from vertical. The force is measured in kilograms since we used a sprint scale to measure the force, but really, this should be in newtons. We loaded the bar to 1 kg, then took this as the base reading. All subsequent readings are given compared to this base. Since we’re measuring at the millimetre level, taking a base reading like this allows us to iron out any slight inconsistencies with the prints. While this method isn’t flawless, the results did prove repeatable and consistent across multiple tests. The first test we did was on different infill percentages. Each bar was printed using grid infill at differing percentages. Here are the results:

Perimeters
The second thing that we looked at was the effect of adding extra perimeters. This simply means that there are extra layers of solid perimeters around the side of the print. In this test, we used 40% infill, with increasing numbers of perimeters.
The below graph shows the impact this had. Here, as you can see, adding extra perimeters didn’t make the structure significantly stiffer (even at higher loads), but it did mean that it would flex further before breaking. This differs from infill, where we found that the amount of flex at the point of breaking was fairly consistent, but the amount of force it took to get there was different.
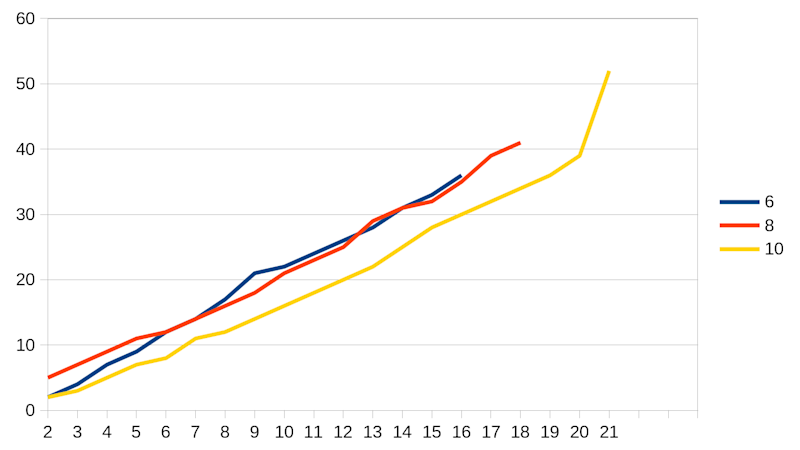
Since we’re also looking at two different ways of increasing the strength of the material, this begs the obvious question as to which is the most cost-effective. On average, each additional 10% of infill added 1.5 kg to the maximum force that could be applied before breaking. It also added 0.96 metres of filament (1.75 m diameter) to the print. This means that we required 0.64 m of filament to add an extra 1 kg to the force required to break the model.
Each two additional perimeters added 1.67 kg to the force, and only took 0.42 m of filament. This means that it only took an extra 0.25 m of filament to increase the force required by 1 kg (though, unlike the infill percentage, the number of perimeters has to be a whole number). Looking at this in isolation, it seems obvious that increasing the number of perimeters is the best option for increasing strength but, as always, it’s worth testing on your particular part.
A Grain of Salt
3D-printing a strong part is a complex process, not least because strength means different things to different people. Your part may be under compression stress, tensile stress (stretching), shear forces, and others – and maybe more than one at the same time. The only accurate way of knowing what the best settings are for printing your piece is to print it with different options and test them out. Hopefully, we’ve given you some guidance of the right places to look, but our results shouldn’t be taken as a general answer to all your 3D printing strength questions.